Imagine you're having a new kitchen installed. We all expect the oven to work perfectly from the first day without any artificial odors and to reach the desired temperature. The refrigerator light should turn on when the door opens, and the exhaust fan should be centered perfectly.
In manufacturing, "First-Time-Right" refers to the ratio of usable parts to total production. Errors and rework are costly, not only in series production but also in toolmaking. Whether a project can be completed successfully or results in costly correction loops is often determined when new tools are started up. The saying, "He who wishes to build high towers must spend long on the foundation" (Anton Bruckner), is especially true here.
Through simulations, different variants and designs can be virtually tested in advance. However, in design practice, there is often a gap between the feasibility analysis (forming simulation) and the assessment of clearance and stroke rate (kinematic press and transfer simulation). Frequently, the production machine is selected based only on the available press capacity and maximum forming force. This simplification can negatively affect tool start-up and increase ongoing production costs.
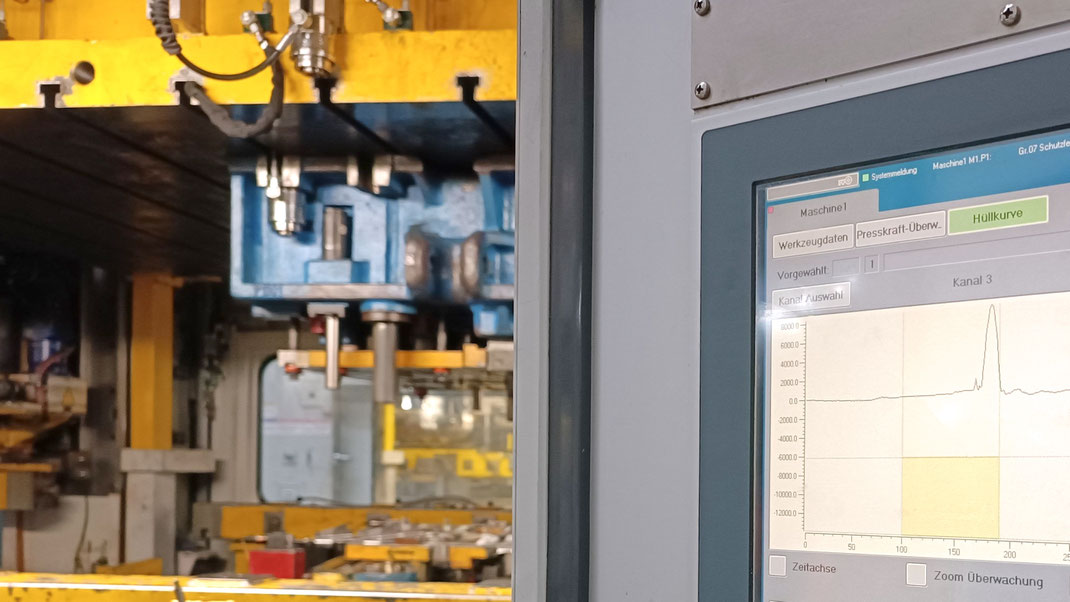
Important Press Characteristics
All input variables and the limits for closing this gap are known from the method plan. These include the forming forces and spring forces as well as their operating zones by means of spring strokes or ram position. This data can be used to calculate the force build-up and the required working capacity (see Fig. 1). The force build-up must be compared with the nominal force- slide position curve of the press in order to avoid overloading the drive kinematics or the drive. The check of the working capacity, on the other hand, ensures the ability of the press to be operated in continuous mode and results in the admissible stroke rate range of the press.
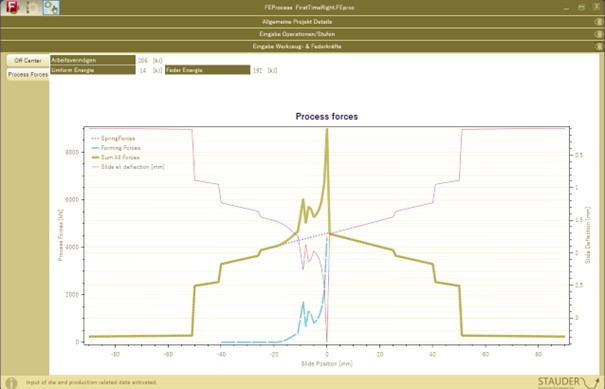
Exceeding the permissible working capacity can cause conventional presses to "starve," preventing automatic continuous operation. In presses with servo drives, the consequences are manifested as exceeded temperature limits, which can usually be compensated for by reducing the stroke rate or changing the ram curve—but at the cost of productivity.
Another aspect is ram tilting due to eccentric forces (see Fig. 2). Different forces at each forming stage cause the ram and tools to tilt, leading to increased wear or quality issues. In extreme cases, exceeding the admissible off-center force can trigger the press’s hydraulic overload protection.
New Insights – Visualizing Force and Press Characteristics
Even in the early layout phase, visualizing force buildup and working capacity can significantly improve design and avoid the described "showstoppers." The visualization of force buildup reveals potential force additions and cutting shocks („reverse tonnage“) impacts. By optimizing the cutting shape and the timing of cutting operations, the cutting shocks and reverse tonnage (see Fig. 3) can be significantly reduced.
Figure 3: Permissible off-center force including forces for each operation in the center of the stage and the resulting eccentric force relative to the press
center. This consideration assumes that all forces act simultaneously at BDC, making it very conservative – in this example, the resulting force exceeds the press limit and is thus not
permissible.
A detailed examination of force buildup over the ram stroke provides more realistic assessments of eccentric forces. For this, the forming forces are examined at the respective ram positions. The result is the progression of the resulting eccentric force depending on the ram stroke (see Fig. 4).
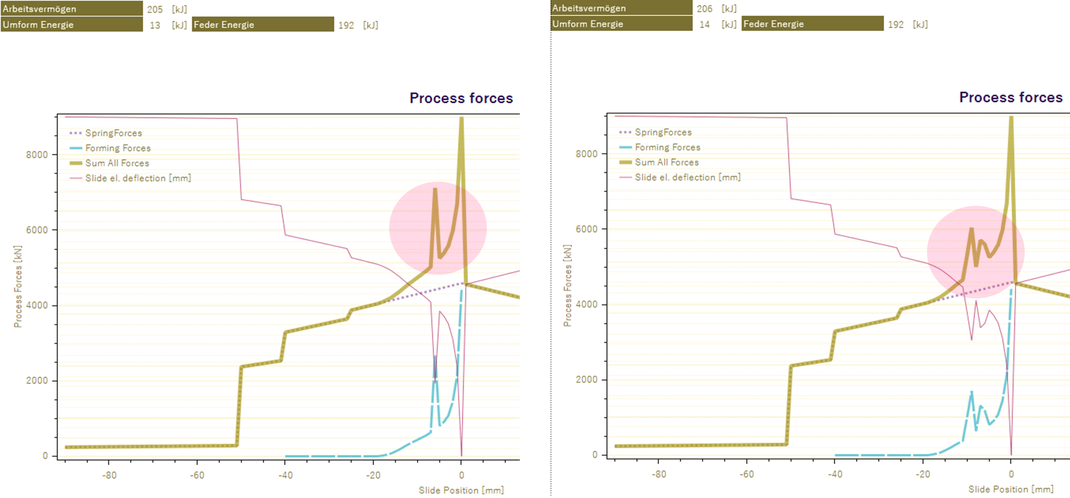
On the one hand, this type of evaluation explains why, in this case, the eccentric force (from Fig. 2) does not immediately trigger an overload stop, and production can thus be planned and run on a press with lower nominal force without additional testing and modification loops. On the other hand, this evaluation offers extended insights. Vertical force progressions are desirable in design. Horizontal force progressions indicate large force shifts across the bolster, resulting in dynamic tilting effects with negative consequences fort he machine/tool lifetime and the forming process.
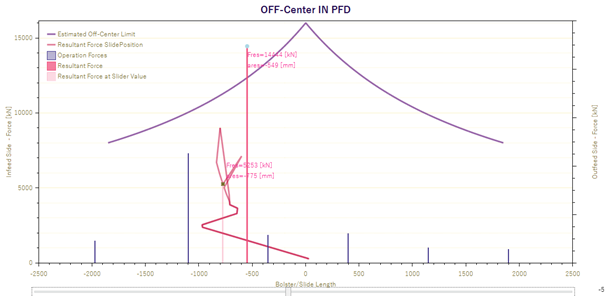
Time Savings in Engineering – Minimizing Production Costs
By taking these relationships into account at an early stage of the design process, the production process is made more robust. Tryout loops in design and die run-in/startup are significantly shortened. In addition, a clever choice of the best suitable press lays the foundation for the lowest possible production costs. The time required for this added evaluation is barely an hour when using suitable simulation software and can be carried out by any tool designer.
"Nothing in life is to be feared, it is only to be understood." – Marie Curie
Take the opportunity to design your next new tool project right from the start! Feel free to contact me so that I can contribute my support as an experienced provider of services to your forming tool development process.
Alternatively, you can increase your own added value by acquiring the necessary know-how through the purchase of an obviFORCE software license. All shown samples are from this software. You can find more information on the homepage - or even better: directly from me! I would be happy to present the software to you and your team personally.