The correct application of interference curves in the age of mechanical presses, e.g. cam-plate-controlled transfer systems was an absolute must of any experienced transfer tool designer. Due to the very limited adjustability of the transfer strokes and the transfer motion timing, dies had to be customized on the clearance conditions of each press. Mistakes in the handling of clearance curves resulted in collisions which could then often only solved by machining the tools or by switching to another press line.
In the age of highly flexible, freely programmable 3-axis transfer systems and the servo press technology, the question of whether a tool is suitable for a press line, due to its specific and on curves-based clearance characteristics, becomes less important. The reason for that is, that clearance can be increased by appropriate machine settings. However, this happens at the expense of the achievable stroke rate! Specifically, this means that whenever machine settings must be changed in favor of more clearance, it will automatically come with less output. In other words, if the tool geometry were optimized for clearance right from the beginning of the design phase, far higher stroke rates could be achieved, or the entire transfer process could be carried out with less vibration and reduced strain on the system!
The correct application of clearance curves is not rocket science. In principle, throughput planning is an accompanying process of tool design.
These are the four principal phases:
1. Creation of interference curves based on the strip layout
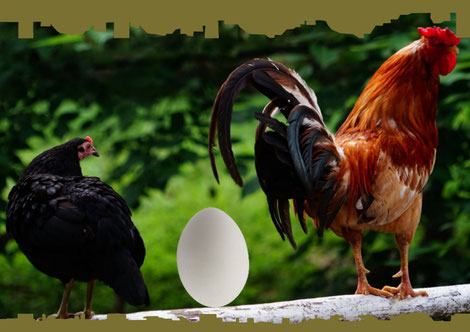
At this stage of the tool design, the designer still has almost all doors open, and he can decide between a variety of possible solution variants, based solely on the component geometry and the manufacturing method.
At the same time, the creation of clearance curves at this stage of the design is also the solution of the old "hen-egg problem" of the tool design because it
offers a possibility to have specific interference curves without in detail designed solid dies.
This makes it possible to optimally adjust clearance curves to the component geometry. Specially it means that the geometry of the tool is predetermined by the
component geometry and the ideal motion curves.
From the height and shape of the component it is possible to derive clearance curves based on assumptions and experience. At this stage it is also possible to
consider the position of guides. Often there is the possibility to place guides between or outside the steps.
By creating these preliminary curves as the basis of the design, a tangible, machine-specific stroke rate estimation is possible – of course assuming appropriate
software tools are available.
2. Throughput planning starts with gripper / shovel design
Many tool designs fail with this step. The gripper ant mounts to the rail, means the design and selection of gripper devices is crucial and should be done directly after the method / strip layout planning, in correlation and connection with the first step. Rather of a fundamental nature is the decision whether active / pneumatic grippers or shovels should be used. On the one hand, the shape of the clearance curves depends on this, and on the other hand, the curves created in step 1 must be attached / positioned on these geometries.
Without this step, the curves also make no sense, because there are no attachment options.
In no case move the design and selection of the gripper elements to the end of the tool design and carry out this step wisely!
3. Application & attachment of interference curves
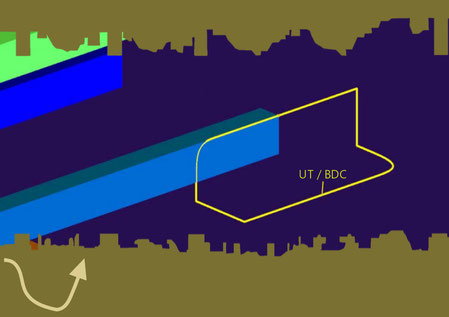
There are different types of clearance curves. You still often see 2D curves for each orthogonal plane. However, there are also real 3D curves, which not only save a lot of time, but collisions can in term be identified much clearer. This 3D clearance curves are a significant relief and are clearly to be preferred - if available.
In both cases, the curves are marked with an attachment marker indicating the BDC (bottom dead center) position. To attach (position) the curves, the tools and the
tooling (grippers and mounts) must be positioned at BDC. This is the attachment position. When using 3D curves, it is important to move the grippers and the gripper rail to this
position!
Following one of the crucial steps: The clearance curves must be attached at several points – means multiple times. It is usually not enough to attach the curves at
one point only since there are several collision critical contours between the gripper rail and the tools. On the other hand, applying the curves too often is not advisable, as this results in a
rather chaotic appearance of the CAD model, and critical areas can be overlooked by the numerous curves.
Overall, this step requires the most experience and imagination since the critical and collision-prone points are not always obvious.
In addition to the theoretical, machine-based clearance curves, a safety distance should be considered by an offset to the original curve.
4. Identifying collisions
After the third step the tool-solid design starts. By e.g. showing / hiding the interference curves of the flow chart, the designer can recognize the movement space of the transfer grippers and mounts. The interference curves describe a taboo space for the tool design. No tool elements may be positioned in these areas.
As a result, an overlap between an interference curve and a tool or equipment contour means a collision.
When checking flow/throughput plans, the plausibility of the created curves should be checked - especially in the context of a design acceptance test. Only then
possible collision areas should be checked/identified.
Decision makers should be guided by the question: "Where is the smallest distance between the clearance curve and the tool" to identify the critical points. These are then also the stroke number
determining contours! ... perhaps this can be redesigned?
Flow planning integrated into the tool design helps you to reduce design time, to recognize errors in good time and to be able to take countermeasures. What matters, however, is that tools become "tailor-made" for the transfer process, thus enabling maximum output and productivity.
Would you like to learn more about optimal and time-saving flow planning? You want to meet your suppliers on equal footing and competently confront them? Would you like to empower your employees to independently identify and implement improvement potential?
Then I have something for you:
Workshop: Interference curves-based flow planning and collision analysis
Contents:
-
Basics & backgrounds of interference curves
-
Approach how to create or specify interference curves
-
Flow planning and collision analysis: handling of clearance curves
- Practical example: How to create and attach interference curves
Facts:
Target group:
Die designers, -planer, -supervisors
Location:
At your premises
Duration:
1-1,5 days
Recommended number of
participants:
4-8 persons
You can send a request at any time via the contact form.