In manufacturing in general, but especially in metal forming, everything focuses on the output performance.
This is not particularly surprising, as it allows the accruing plant allocation to be divided among more workpieces, thus reducing the production costs per piece.
The increase in the cycle rate of a production line therefore has a direct effect:
- Reduction of manufacturing costs per workpiece
- More free production capacities
► Higher profit!
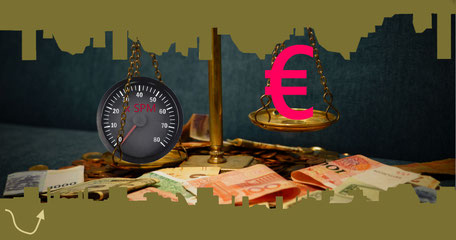
"Increasing the stroke rate outweighs the costs for process optimization."
There are many ways to increase the output of a production line:
- New investment in modern machine technology for higher productivity
- Updates & upgrades of existing installations (retrofit)
- Improvement of tools (e.g. modification or new development of tools)
- Improvement of processes directly at and around machines (value stream design, OEE optimization)
While new investments and retrofits generally require long-term actions, a significant increase in output can be achieved with relatively little effort by improving the processes around the machine.
Especially on stamping presses, an increase in stroke rate can be achieved by optimally adjusting the process parameters of coil feed, 3-axis transfer and press.
But how large must the increase in the stroke rates be in order to make the costs for the service work worthwhile?
A simple and conservative calculation of the economic success of such a measure can be based on the hourly rate and the annual production time of the respective production machine. The annual operating costs can be calculated from these values. The optimization results lead to an increase in machine productivity. Thus, the effect of an increase in the stroke rate can be shown in a calculatory profit. It is important for the calculation to determine the improved overall production volume of the plant from the result of the optimization and the machine occupancy time of the respective tool.
On the cost side, the costs for the optimization service and the resulting loss of production must be considered.
This approach is particularly conservative, since by assuming an hourly rate the costs, but not the profit achieved with the manufactured workpieces is considered. This type of calculation is therefore particularly suitable for the qualitative assessment of the production improvement.
On the right side you can see an exemplary calculation of the result of a process optimization.
It was assumed that a total of 10 tools are run on the line. In total, the stroke rate of five tools was increased by 10%, 15%, 5%, 5% and 10% respectively, which leads to a calculatory increase in production volume of 5.75%. (in reality often much higher values are achieved)
With the exemplary and fictive assumed values for the hourly rate, this results in an imputed revenue of the optimization measure of approx. $ 100,000. Related to the costs for the measure, this means a return on investment of 330%.
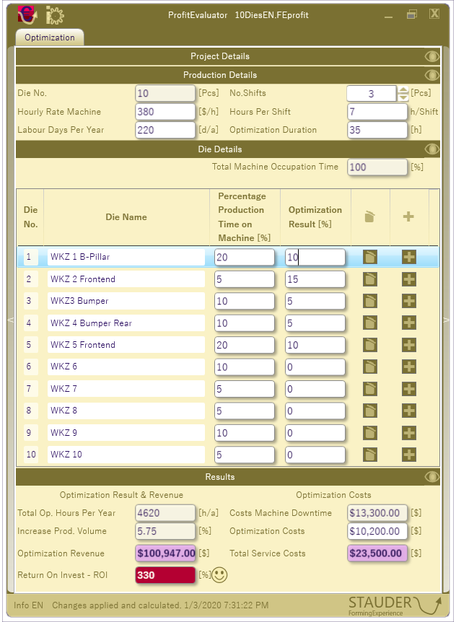
This is impressive - and can be easily understood at any time by using a spreadsheet. Although this result is conservative due to the simplified consideration over the machine hourly rate, interesting conclusions can be drawn for the planning of the optimization service.
1. Die selection / priority:
The tools with the highest demand / production volume are usually selected for the optimization service. In practice, a considerably larger increase in the number of strokes is often achieved for tools with a low production volume. This is probably since less attention is paid to these tools. Here in particular, the features of servo presses can be used particularly well and thus significant increases in production volume can be achieved despite the low occupancy time.
2. Costs for loss of production:
The optimization activities at the machine need time, which leads to a production downtime. This is the main cost factor in relation to the total costs.
By means of a virtual flow simulation, most of the required parameters, especially those relevant to clearance set-up, can be determined virtually and in advance of the optimization service. In this way, the downtime can be minimized and the additional investment of such a service can be justified.
Are you in charge of the press-shop, process and output optimization or tool design and would you like to increase the output of your plant? ...I look forward to receiving your message and will be happy to discuss the best approach for your case together with you.
I would like to thank all readers of my articles for their interest and feedback and wish you a successful, innovative and optimal year 2020.
Kommentar schreiben